The power is out, and you need to order a pizza, and your phone is dead! Thank goodness you already built a hand crank phone charger as part of the summer 2024 Clean Energy Deep Dive. This apparatus turns a cheap plastic gear motor and a simple regulator circuit into a slow but effective phone charging appliance, and even includes measurement points so you can calculate how much power your cranking efforts produce!

Safety
The electronics part of this build involves a bit of thru-hole soldering with an iron. We don’t have certifications in place as of yet for this process, so students should be closely supervised throughout. There are two main concerns here:
- high temperatures: soldering irons run at 750 F or higher, which can cause instant burns and may contribute to starting fires in the right conditions. When not in use for a brief period, they must be returned to their stands; when not in use for an extended period, they must be shut off. While soldering, students must be seated and paying close attention to the task at hand, and must wear safety glasses in case of splatter. Soldering should only be performed on a suitable surface with sufficient work-holding, such as a Stick Vise on an anti-static mat.
- fumes: while not sufficiently hazardous to necessitate the use of extensive PPE (such as a respirator), the fumes given off by vaporizing flux can irritate lungs and cause health issues with long-term exposure. Students must always use a fume extractor which is placed close enough to the work area to actively extract fumes. Note that activated carbon filters mostly knock out heavy particles and dilute remaining fumes into room air, so the back end of the extractor should be aimed away from students.
Beyond these two concerns, students should also be careful trimming leads as the ends can fly off; keep the safety glasses on and use hand tools with care. At this point all of the leaded solder should be purged from the work area, but instructors should double-check before soldering starts. Wash hands when finished.
Build It!
Classroom assembly involves soldering on a few thru-hole parts and fitting together the generator apparatus. This should take pairs of students a half hour, give or take.
Tools and Materials
- Tools, which can be shared between groups
- soldering iron
- tweezers
- flux
- lead-free solder
- safety glasses
- soldering surface
- work-holding device (such as a stick vise)
- multimeters and probes (optional, for quantifying device performance)
- wire flush cutters
- small flat-head screwdriver (for terminal blocks and mounting PCB)
- Materials, needed for each hand crank phone charger
- partially assembled regulator board
- thru-hole electronic parts
- USB receptacle
- terminal block
- header
- shorting jumper
- 6-32 x 5/16” pan head slotted machine screw
- 3” C-clamp
- laser cut wood parts
- base piece, 1/4” plywood, with 6-32 T-nut preinstalled on the back
- small gear, 1/8” plywood
- large gear, 1/8” plywood, glued to shaft and handle dowels
- bushing, 1/8” plywood
- handle pivot sleeve
- yellow right-angle gear motor from amazon
- small zip-tie
- an inch or so of 1/8” aluminum craft wire
- USB-C or Lightning cable for phone
Construction
Electronics - We already did this for you :)
- Insert the terminal block into the circuit board with the wire openings facing away from the regulator. Use a bit of blue masking tape to temporarily hold it in place.
- Flip the printed circuit board upside-down and secure it in the stick vise.
- Add a drop of flux to each pin. A tiny bit is sufficient.
- Tin, wipe clean, and re-tin the soldering iron tip.
- Solder the exposed pins one at a time by holding the iron to the board so it touches both the pin and the pad, and then feeding solder into the joint until the fillet is shiny and slightly concave. Remove the iron after feeding in the solder.
- Carefully snip the leads flush using flush cutters.
- Remove the blue tape.
- Repeat for the USB receptacle, using caution as the metal housing will get hot during soldering. Start with the two outer structural pads and then solder the four pins.
- Carefully trim the header using flush cutters into three two-pin units. Repeat the soldering process for the three measurement headers.
- Install the shorting jumper on the current measurement header marked Iout. Note! Do not short out the two voltage measurement headers (marked Vin and Vout)! Those two headers should be left free.
- Ask an instructor to inspect your work before moving on. Good job!
Apparatus (Students start here 🙂)
- Line the circuit board up with the marked outline. The thru-hole soldered connections should fit into the holes in the base board.
- Screw the 6-32 x 5/16” pan head slotted machine screw into the mounting hole with the pre-installed T-nut on the back and tighten to secure the board.
- Position the motor under the board with one of the shafts sticking up through the hole, and the wires on the underside.
- Secure the motor with a small zip tie through the two mounting holes and trim the zip tie flush. Make sure to pull it good and tight!
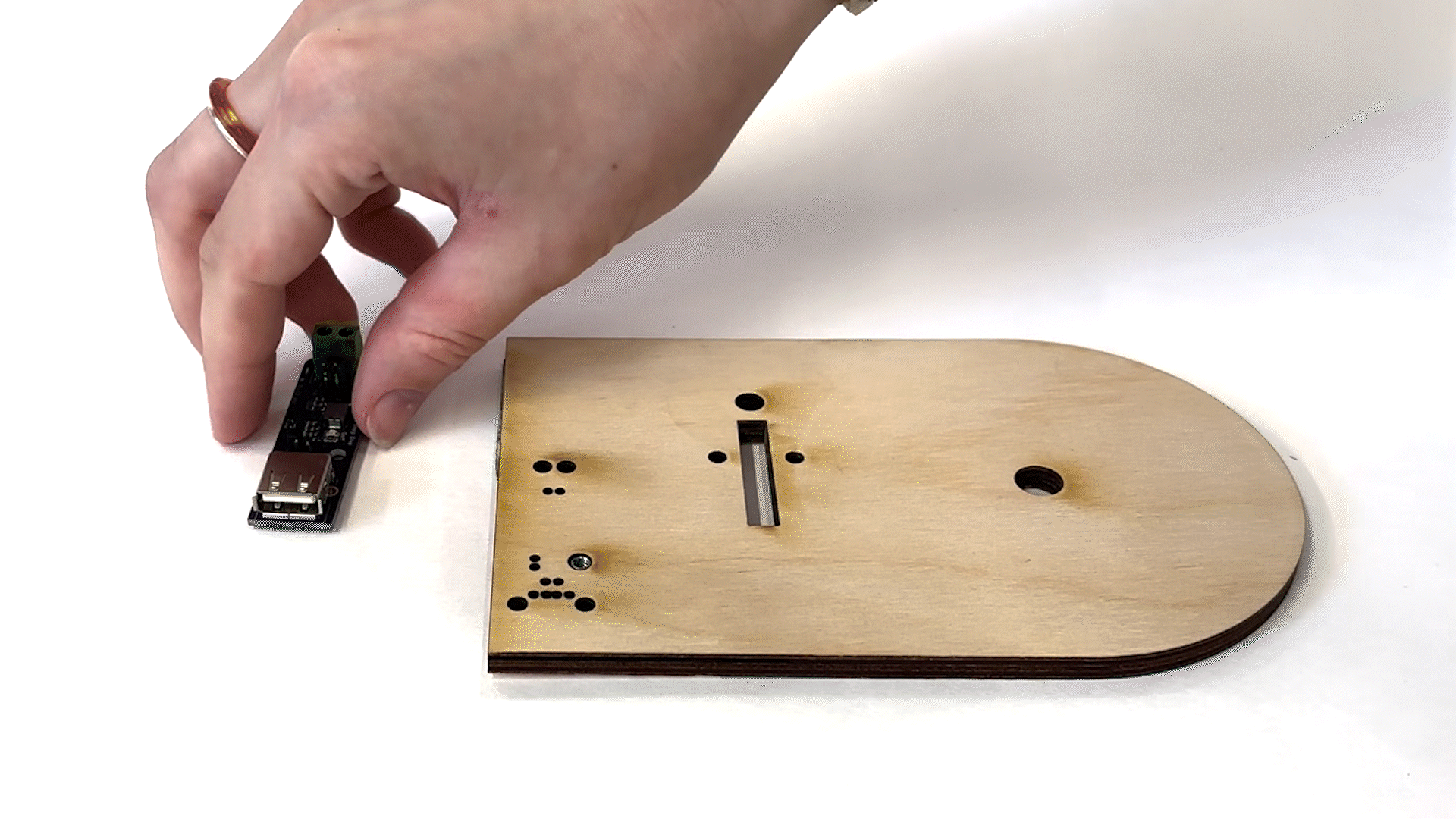

- Press the small gear onto the motor shaft. It should be a tight friction fit. Don’t bottom the gear out against the back plate; there should be a slight gap so it can rotate freely.

- Drop the large gear into its mounting hole and rotate until it meshes with the small gear. Push the bushing onto the rear shaft, leaving a slight gap so the gear can rotate freely.
- Secure the bushing by inserting the aluminum craft wire and bending the ends into an S-shape. Be careful, the craft wire may be a bit sharp from cutting.

- Connect the red and black wires from the motor to the terminal block on the circuit board. Red should go to “+”, black should go to “-”. To do this, insert the metal pin into the open gate on the side of the terminal block and tighten the screw until it grips the pin. Test the connection by gently pulling the wire; if it comes free, loosen the screw and try again, tightening a bit more this time.

- Clamp the apparatus to the side of a table using a C-clamp as shown. To keep the assembly from rotating, gently push the side of the motor against the edge of the table top. Tighten the clamp securely.
- Drop a handle pivot sleeve onto the handle; this will make long generator sessions immensely more comfortable!
- Give the generator a test run! Turn the handle clockwise; the green LED on the circuit board should light up. Note that turning the handle counter-clockwise won’t light the LED, but won’t damage the circuit either.

Use
Charging Phones
Plug a USB charging cable into the onboard receptacle, and then into a phone. Turn the crank. The phone should start (slowly) charging! Huzzah! How long does it take to gain one percentage point? Can you feel the phone switch charging modes?
Measurements
The PCB has three onboard headers: one for measuring the input voltage directly from the motor/generator, one for measuring the output voltage at the USB receptacle, and one for measuring the current consumed by the thing plugged into the USB receptacle.
- Measure input voltage
- Measure output voltage
- Measure current
- Calculate output power
- Estimate phone battery capacity
Connect a multimeter to a cable that ends in a pair of header sockets, noting which connects to the positive terminal. Slide the positive header socket onto the Vin pin marked “+”, and the negative header socket onto the Vin pin marked “-”. Set the multimeter to 20 V DC and make sure the multimeter positive lead is connected to the voltage measurement terminal. Turn the crank clockwise: you should see up to ~9 V DC depending on RPM, and the LED should turn on at ~3 V DC. What happens to the reading if you turn the crank counter-clockwise?
Follow the instructions for measuring input voltage, but connect the multimeter to the Vout header instead. What voltage do you see when you turn the crank clockwise and the LED lights up? What about counter-clockwise?
Remove the shorting jumper from the Iout header and connect the measurement leads as described above. Make sure the multimeter positive lead is connected to the current measurement (mA) terminal. Set the multimeter to 200 mA DC and connect a load like a phone to the USB receptacle. Turn the crank clockwise to charge the phone: what happens to the current reading? Does it change when you turn the crank faster? What about when the phone changes charging modes, or when you disconnect the phone?
Connect the output voltage and current measurements simultaneously, as described above. Attach a phone to the USB receptacle and turn the crank clockwise. Write down the voltage and current readings, then multiply them by each other. Since the current is displayed in milliamps, multiply the result by 1000 to see output power in watts (since P = I * V). How many watts are you producing while the phone is charging? What about when the phone changes modes?
Connect the meters as described for calculating output power. Turn the crank steadily until the phone charge percentage increases by 1%, then start a stopwatch. Write down the output voltage and current when they are at steady-state. Stop the timer and crank when the phone charge increases by another 1%. Multiply the calculated power in watts by the number of hours (minutes / 60): this is how much energy you sent to the battery in watt-hours. Since this accounts for 1% of the phone battery capacity, multiply the energy value by 100 to estimate the phone battery capacity in watt-hours. How does this compare with your phone’s published specification? Why would it be different? How could you improve the estimate?
Background
Circuit
The hand crank phone generator circuit is a buck-boost switching voltage regulator based on TI’s TPS63061 integrated converter, a tiny part which only requires a few external components to use. I selected this chip because it is (a) ubiquitous and available ($2.70 in single qty from Digi-Key as of this writing); (b) easy to use, taking advantage of TI’s great documentation and example circuits/layouts; and (c), fits our electrical needs: a wide range of input voltages (2.5 - 12 V DC, roughly the generator range), a fixed output suitable for phone charging (5 V DC), and plenty of current capacity. The tiny 3x3 mm DSC 10-pin package can be annoying to solder even with stencils and paste, but it’s easy enough to rework when inevitable solder bridges crop up.
I designed the circuit in KiCad, a fantastic open-source electronics EDA tool. It only has a few additional components beyond the example circuit from the datasheet: an input screw terminal block; an output USB-A receptacle; current and voltage tap headers; a power-on LED with current-limiting resistor; and, crucially, a reverse polarity protection Schottky diode on the input, since students are guaranteed to turn the crank both directions at some point. Otherwise, I used the recommended components and close to the recommended PCB layout as described in the datasheet and the circuit seems to work well enough.
Routing the board was particularly fun. Due to the frequencies and powers involved, switching regulator circuits benefit from fat traces and lots of vias. I made extensive use of polygon fills for the high-power traces, leading to a board that has a lot of nifty shapes on its top copper layer.
Crank Mechanism
The crank mechanism mostly serves to speed up the gear motor using a 3:1 wooden spur gear arrangement. One can certainly drive the gear motor directly and generate a bit of power, but getting a few shaft rotations from each crank handle rotation makes generating useful power much easier. This part of the apparatus also can be used to teach students basic concepts about gear trains: reduction ratios, torque vs speed tradeoffs, wear, backlash, direction reversal from gear meshing, and the like. The base plate also provides a sturdy base for the circuit and gearbox, and allows the apparatus to be securely clamped to a table for longer term use.
The crank mechanism was designed in Onshape which conveniently includes a spur gear creation tool, meaning we don’t have to sort through parameterizing involute tooth profiles. The complete CAD assembly is available for export here.
Pre-Class Fabrication
Files
[TODO: upload after verifying new boards and full assembly works!]
Ordering
The circuit boards are designed with relaxed design rules, so most reputable commercial fabricators should not have any issues with spacing or hole diameters. However, you should specify ENIG (electroless nickel immersion gold) plating rather than HASL (hot air solder leveling) to make soldering the buck/boost converter a bit easier. Make sure the substrate is rated for RoHS reflow temperatures; most FR4 is fine. Otherwise, standard two-layer 1/16” (1.6 mm) FR4 will do nicely. Some services like OSH Park accept KiCad files directly, while others like PCBway and JLC prefer Gerbers and drill files. These live in the /fab folder and generally get zipped prior to submission to the fabricator.
You’ll want a stencil as well for reflow soldering! OSH Stencils is a great and fast vendor; the 0.003” polyimide film stencils are great. Some PCB vendors will provide a stencil along with the boards for a nominal fee; if you go this route, just avoid ones with the enormous frame. Stainless steel is fine, but see if you can get thin stock (0.003” or less) as the standard 0.004” caused more solder bridges than I’d prefer. I suppose this could be fixable in the solder paste aperture department.
As of this writing, all of the electrical components are available on Digi-Key using the links that live in the Links field of the BOM. This *.csv file lives in the KiCad project folder. Some parts, like headers and resistors, can be freely substituted; use caution on others and be sure to check footprints for compatibility. Swapping the chip will probably necessitate a full redesign.
Other things to buy, many of which we likely already have floating around the basement:
- 1/8” plywood, exact thickness not critical
- 1/4” plywood, exact thickness not critical
- 1/8” aluminum craft wire
- 3/8” (9.5 mm) dowels
- 6-32” x 5/16” slotted pan head machine screws (these are good)
- 6-32” tee nuts (these are good)
- amazon DC gear motors, the yellow kind with two shafts, possibly branded AEDIKO TT
- zip ties, 3 mm (~1/8”) width
- wood glue
- sand paper
- 3” C-clamps
- solder paste: get a reputable RoHS paste and keep it in the fridge. SAC305 T4 from Chip Quik is a good bet.
- paste flux in a syringe, also Chip Quik
- fine RoHS solder wire, SAC305, also Chip Quik
- a fresh Hakko chisel iron tip, if the ones in the lab are worn out or overly oxidized
- things to make up measurement multimeter leads: screw terminal banana plugs, stranded wire, socket jumper wires that can be chopped in half, and a bit of heat shrink tubing
Electronics Pre-Assembly
Take the solder paste out of the fridge so it can warm up a bit.
Set up a pasting station by taping 1/16” acrylic L-panels (or spare 1/16” FR4 boards) to a table so that the to-be-populated PCBs fit tightly. Create a tape hinge for the stencil, align its apertures to the PCB, and tape it to the acrylic panels so it can be easily lifted to switch boards. [TODO image of pasting setup]
Insert a PCB, fold the stencil down, dispense a bead of paste, and carefully squeegie the paste into the apertures using a credit card or paste spreader (which are often just blank credit cards). Carefully lift the stencil up and inspect the paste; if it is smudged or irregular, wipe the board off and start again. [TODO image of pasted board]
Place the components one by one, starting with the buck-boost controller and moving outwards. Due to the likelihood of solder bridges, I suggest DNPing (do-not-populate) one each of the 10 uF and 22 uF capacitors that are closest to the chip; they can be hand-soldered later. Pay careful attention to polarities: the Schottky diode, the LED, and the chip all need to be placed in the correct orientation. Check diodes with a multimeter in diode test mode if you are unsure! [TODO image of assembled but unsoldered board]
Run the board through a standard RoHS reflow cycle. Our modified toaster oven is a perfect fit for this, or you can use a hot plate as the board only has components on one side, or you can just hit it with the hot air reflow station until all the parts are thoroughly soldered. [TODO: gif of board soldering in reflow toaster]
If you like, you can test the board for functionality: attach a variable power supply to the input pads and set it to 3-12 V DC, and check for output voltage at the Iout + and any convenient ground terminal. You should get a steady ~5 V DC within the full input voltage range, and the power LED should glow. The PCBAs (-A for assembly!) are ready for students to install the thru-hole components!
Other Fabrication Tasks
- Laser cut the base out of ~1/4” plywood, and all other parts (large gear, small gear, bushing) out of ~1/8” plywood.
- Hammer a T-nut into the back of the base, double-checking orientation with respect to the asymmetrical holes and mounting features. [TODO image]
- Cut two dowel sections to 1”.
- Sand the dowel ends down a bit if needed for fit, and then glue them into the holes on the large gear, one on top and one on the bottom.
- Test fit the large gear to the base with the bushing, mark the exposed dowel end, take the assembly apart, and carefully drill a 1/8” hole through the dowel so you can secure it with a loop of craft wire. Once you’ve measured this once (it depends on plywood thickness), you can drill other dowel blanks prior to gluing; just be sure to mount them the correct way! [TODO image]
- Cut sections of 1/8” aluminum craft wire to ~1”, and sand the ends down to reduce the risk of cuts.
Kitting
If you like, you can kit all of the parts together into a bin that can be passed out to groups; alternatively, students can fetch bits and pieces from a common materials library as needed during fabrication.