If you want to make professional-quality relief prints, you should consider using a terrific material we learned of recently (thanks Barbara!) called Gomuban. It’s not particularly cheap, but the green side holds a sharp edge quite well, deforming minimally even when used in a press. It is easy to carve by hand with printmaking tools. We wanted to try using it in the sketch-to-stamp workflow we perfected at Haystack which uses linoleum blocks and a desktop mill.
Traditional rotating-bit machining isn’t a great process for flexible and squishy materials. We ran a few tests on stamp rubber months ago and found it tends to deform around the end mill as it cuts, producing some chips but also resulting in an inconsistent edge with overhangs and fussy flaps that don’t clean up easily. Unfortunately, a first test of Gomuban using linoleum-friendly machining parameters produced a similar result.
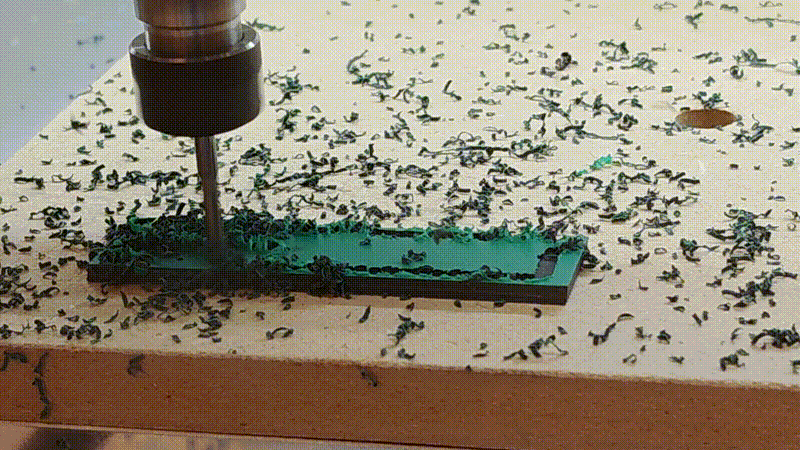
I made a quick G-code file to produce a series of lines at varying depths, thinking perhaps the depth of cut could be moderated to reduce tearing, particularly in the crucial green layer. The first chunk initializes the machine, turns on the spindle, and sets the coordinate system, while each subsequent 4-line block lifts the spindle to Z +3 mm, fast-traverses to Y +2 mm and an increasing X value, drops the Z-axis in 50 µm increments, and machines a 20 mm long line in the Y+ direction:
%
G17
G21
G40
(G49)
G54
(G80)
G90
G94
F600
S10000
G00Z3.0000
M03
G00Z3
G00X2Y2
G01Z-0.05
G01Y20
G00Z3
G00X4Y2
G01Z-0.1
G01Y20
G00Z3
G00X6Y2
G01Z-0.15
G01Y20
G00Z3
G00X8Y2
G01Z-0.2
G01Y20
G00Z3
G00X10Y2
G01Z-0.25
G01Y20
G00Z3
G00X12Y2
G01Z-0.3
G01Y20
G00Z3
G00X14Y2
G01Z-0.35
G01Y20
G00Z3.0000
G00X0.0000Y0.0000Z3.0000
M05
M30
%
Then I tried the file a few times with different mills. I noticed that the Z-zero point seemed a bit off on the first two runs; I think the zeroing probe compressed the material a bit and gave a false reading, so I manually re-zeroed for the latter two by turning the spindle on and manually jogging the Z-axis down until I observed contact.
Another test with a 1/32” ball mill seemed particularly good; the 0.2 mm and 0.25 mm depth settings (third and second from the right, respectively) seemed promising enough to try on a design:
Unfortunately, running the same design at a variety of feed rates didn’t help much; none of these are sharp enough for printing, and they don’t de-fuzz with a stiff brush like linoleum:
And then, progress! I tried something I’ve been scheming for awhile: cooling down the substrate to stiffen the plastic up prior to machining. I did this in-situ, by spraying the Gomuban with a few shots from an upside-down duster. Proper freeze spray is a much better idea, both from a consistency and a health perspective, but this worked in a pinch for testing.
I tried a back-to-back test with one of Barbara’s seal patterns scaled to ~3/4”, using a 1/32” ball mill for the whole operation. Parameters are 0.25 mm (0.01”) depth of cut, one pass, 30% stepover, 20 mm/s feed rate, 5 mm/s plunge, 10k RPM. I still got a tiny bit of fuzzing with a flat end mill, so at the very least it’s probably worth using a ball mill for the first outer pass.
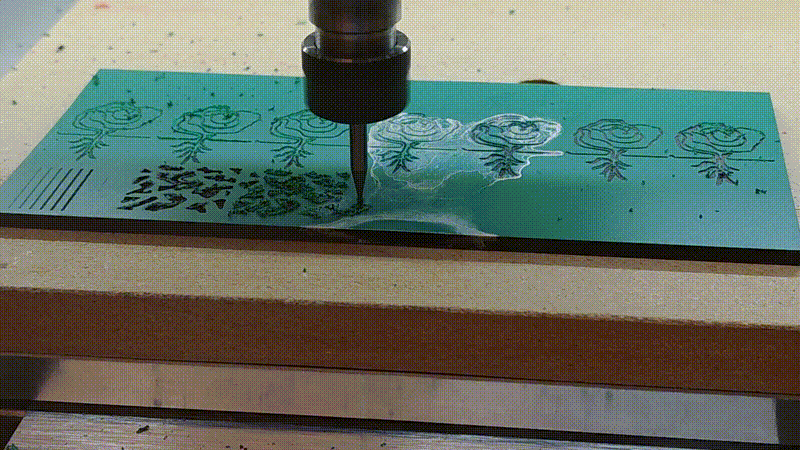