- What is Finishing a 3D Print?
- What are we making?
- What Tools and Materials to Use
- 🚨 SAFETY WARNING 🚨
- TEMPAD PROJECT
- Setting Your Model to Print
- Cleaning Up Your Prints
- Sanding Your Prints
- Sanding
- Applying Filler Primer
- Applying Filler Putty
- Painting Your Prints
- 🚨 Before We Begin 🚨
- Priming
- Painting
- Painting Metallic Parts
- Optional: Sealing
- Incorporating Other Materials
- Laser Cutting the Wood
- Milling the Acrylic
- Creating the Buttons
- Assembling Your Parts
- Assembling the Time Turner
- Assembling the Keypad
- Assembling the Screen Lid
- Final Assembly
What is Finishing a 3D Print?
A great fabrication medium to incorporate into your business is 3D printing. Whether selling a 3D printed item, creating a master model to be molded, or any application, often you will need to go beyond a simple raw print. Finishing, or post-processing, a 3D print is the process by which you go from a raw 3D print straight from the machine to a final product by means of sanding, painting, implementing other materials, etc.
What are we making?
This project will cover the basics of finishing a 3D printed item by finishing a replica of the TemPad from the Marvel series Loki. The skills you’ll learn in this tutorial will be easy to translate to other projects you may create, and will hopefully inspire you to learn more beyond what is covered here about post-processing.
What Tools and Materials to Use
For this process, we will be using a variety of tools and materials to finish our prints. You may use slightly different materials, you may even omit some entirely. But this is what you can generally expect to use for finishing a 3D print.
Tools:
- 3D Printer (Dremel 3D45)
- Cutting Tools (ex. X-Acto Blade, Utility Knife, Flush Cut Pliers)
- Sandpaper, both rough grit (80-120 grit) and fine grit (220-400 grit)
Materials:
- PLA Filament
- Glazing Spot Filler Putty
- Filler Primer
- Spray Primer and Paints (for this project we will be using Gloss Black, Brass Gold, Green, Pink, and White)
- Super Glue or 2-Part Epoxy
Additional Tools and Materials for this Project:
- Nomad 3 CNC Machine
- Glowforge Laser Cutter
- 1/16 in. Black Acrylic Sheet
- 1/8 in. Medium Walnut Plywood
- Neodymium Magnets
- Rubber Button Pads
- Printable Vinyl Sheet
- Black Adhesive Vinyl
- 3mm Steel Rod
- Masking Tape
🚨 SAFETY WARNING 🚨
- Many of the materials we will be using have strong fumes or fine particulates, such as plastic, that are toxic and dangerous if inhaled. Make sure to always wear disposable gloves, a respirator mask, and safety goggles when handling these materials.
- When using spray paints and primers, always make sure the nozzle is facing the opposite way spray away from your body and in the direction of any wind or breeze there may be, otherwise you may get spray paint on your clothes or skin.
- When handling sharp tools, be very careful and conscious of where your fingers are in relation to the blade. Always cut away from yourself, never towards.
- When handling the filler putty and spray paint, make sure to regularly put on fresh gloves when yours become too dirty. Do not touch your face or body while wearing safety gloves.
TEMPAD PROJECT
Setting Your Model to Print
First things first, we need a 3D print. Whether you find a model online, commission a 3D modeler to create one for you, or model one yourself, you will want to follow our 3D PrinterOS Tutorial in order to properly print your model(s) in our 3D printer farm. This is the first step in prepping and finishing our final print.
Cleaning Up Your Prints
- Using a variety of tools, such as needle files and X-Acto blades, carefully remove the brims of the prints and clean up the edges.
- Using a set of flush cut pliers, remove all support material.
- Be sure to test fit the pieces as you go. If some parts don’t fit quite right we may be able to correct that during the sanding process.
- Now is a good time to glue the neodymium magnets in place.
Sanding Your Prints
Before we can even consider painting, we need to get these parts to be smooth as metal to match the look we’re going for. For your project, maybe you dont want a mirror smooth finish and prefer a rougher surface, or maybe even wanna take advantage of those print lines and go with an unsanded final product. But if you choose to sand, here’s how to go about it.
Sanding
- To begin the process, you want to start at a low grit sandpaper and move your way up to a higher, smoother grit. Starting with anywhere from 120 to 150 grit, begin by sanding opposite of the “grain” (the direction of the print lines).
- Follow up with a 320-400 grit sandpaper, following the same sanding direction to smooth out the rough surface by the rough grit.
- If there are any lines or smaller details that you can’t sand with the sandpaper, you can use a needle file to get into the smaller bits of the print.
- At this stage, we can also super glue our neodymium magnets in place to connect the keypad and the Time Turner. This way the magnets will be hidden by the paint job we will later apply.
Applying Filler Primer
Once you have your pieces sanded, it’s time for the first round of filler primer. This will fill in some of the scratches and lines left behind from sanding, and will also show any spots you may have missed or gaps in the print that were too fine for the printer to fill.
- 🚨 Make sure to be wearing safety equipment for the next steps, it is now crucial to your safety🚨
- Keeping the can about a foot away from the prints, apply the filler primer in short vertical spritzes. Don’t apply in a long spray or you may cause drips and runs in the primer.
- Give the pieces about an hour to dry in a well ventilated area. If its cold, you may have to give it more time to dry.
Applying Filler Putty
At this stage, you may notice that some spots are not smooth. Maybe there are some scratches from the rough grit sandpaper that weren’t smoothened out, or perhaps some print lines that were missed in the sanding process. We can cover these spots up using a glazing spot filler putty.
- Using a sharpie, mark any spots that need to be smoothened.
- To fill in or cover these spots for easier sanding, apply a thin layer of the filler putty. The more you cake on, the longer it will take to dry. A thin layer should do just fine, and if you need to apply more than wait for the first layer to dry.
- Using the fine grit sandpaper, lightly sand down the filled in areas. If you use the rough grit, you will likely undo much of the work you have done and add more scratches.
- Once again, apply a layer of filler primer to the prints.
You can repeat the putty and primer steps until your prints are as smooth as you would like them to be. When you no longer see any lines or scratches, lightly sand the entire surface with the fine grit sandpaper to smoothen out the rough surface the filler primer leaves behind. We are now ready to begin painting
Painting Your Prints
Once you have gone through the sanding process, you should have your prints to your desired smoothness. Now is the time to paint your pieces. For this project we will be using Rustoleum spray paints, however you can use any brand or type of paint you want, such as airbrush or brush-on.
🚨 Before We Begin 🚨
Painting your prints is what will make or break the process, so its important that we make sure to do it properly. Some things to keep in mind when spray painting:
- Never spray without wearing some kind of lung protection, such as an N95 mask or air respirator.
- Make sure you’re spraying in a well ventilated area, whether that is outside in good weather or in a ventilated spray booth, such as our Paint Room located in the Fab Lab.
- Make sure to ask one of our educators for help turning on the vent system if you do not know how.
- Always wear some form of eye protection to prevent getting paint in your eyes. Eyeglasses/sunglasses will not cut it, you should be using proper safety glasses.
- When spraying, make sure to be wearing disposable gloves to protect your hands from overspray and the paint from fingerprints and smudges.
- When spraying, keep the can about one foot away from your prints while moving at a constant steady pace to prevent drips, runs, and pooling of the paint. Better to apply a couple lighter coats to ensure full coverage than to do one heavy coat and have to correct it later.
- Allow your paints to dry before light handling and fully cure for the full time listed on the can before moving on to the next step. In our case, we’ll be using Rustoleum brand spray paints which require a full 24 hours to cure fully.
- Drying time and curing time are different. Drying time is for when pieces will be dry enough to handle and recoat, while curing time is to allow the paint to reach its peak hardness.
Priming
Before we apply our color paints, we want to apply a primer coat. This will not only help the paint stick better to the surface of your print, but it will make it all one even flat color so that the paint remains consistent across all pieces. Different undercoats/colors can affect the same paint differently, so better to make it all the same.
- For smaller parts and any pieces that you may need to move around while painting, tape them down onto a piece of cardboard or poster stock. This will allow you to move the parts around for ease of spraying without having to handle them directly while wet.
- Using Rustoleum Flat Gray Primer, apply an even coat across all pieces. We want to avoid drips and runs at any and all stages, so make sure to keep the can at a distance and moving while spraying.
- Allow these pieces to dry for at least 30 minutes before handling, and for 24 hours before moving on to the next step.
Painting
Once the primer has fully cured, we can now begin painting our pieces.
- For this project we’ll once again be using Rustoleum brand spray paints.
- For the panels, we will be using Gloss Meadow Green
- For the number and direction buttons, we will be using Flat White
- For the leftmost buttons, we will be using Gloss Berry Pink
- Spray these parts by color away from other pieces to avoid overspray.
Painting Metallic Parts
When you’re painting with non-metallic paints, all you truly need is a simple primer undercoat. However, when painting with metallic paints like gold or silver, a simple primer coat won’t cut it. To maintain a nice shiny finish, you would use a Gloss Black paint as an undercoat.
The process is very much the same as the previous section. Once the primer coat has cured after 24 hours:
- Apply a light coat of the Gloss Black paint. Recoat every 30 minutes until you have a full even coat.
- After the Gloss Black has dried for 24 hours, we can now apply a coat of Brass Gold paint. Metallic paints tend to come out more speckled, so you should have an easier time getting a full coat in one go with no drips.
- If you need to paint any parts multiple colors, you can use masking tape to cover any areas you want to remain unpainted and spray the exposed parts. Just make sure the previous coat is fully cured or else the tape may damage the paint.
Optional: Sealing
Once you have painted all your parts, you have two options. You can move on to the assembling your parts, or you can now apply a coat of sealer.
Spray sealer is able to not only protect your paint from damage down the road, but also provide a matte or gloss finish to the look of your prints. Certain paints won’t require a sealer, but for others its a good practice to protect your paint job you worked so hard on.
Like the spray paints, just apply from a distance in small sprays. Spray sealer can drip much easier and more noticeably than paint when applied too thick, so be very careful during this step if you choose to seal your pieces.
Incorporating Other Materials
While it is certainly possible in most cases to make your project entirely 3D printed, often times you will achieve a better result when you incorporate other materials. For example, why bother printing and painting panels to look like wood when you can just use wood from the get-go? For this project, we will be using wood for the wooden panels, black acrylic for the screen and dial, and other miscellaneous materials for different functions.
All materials are determined by the needs of the project. For this project, a retro-style digital device, we use materials such as acrylic to simulate the different parts of the original prop for aesthetic purposes, and miscellaneous materials such as magnets for functional purposes. You will need to decide what you’ll need for your project based on your needs for it.
Laser Cutting the Wood
As mentioned above, the original prop has many wood panels on the surface, so to better match that look, we’ll be using 1/8 in. medium walnut plywood. The darker wood will better match the look of the original prop without any further work needing to be done on it.
- Uploading an image of the front of the panel board of the 3D model to Adobe Illustrator, I traced an outline for the wooden panels measured to fit within the empty spaces, and saved as a .SVG file.
- When creating something to be cut on the laser cutter, you should make sure your drawing tools are set to red so that the Glowforge recognizes these lines as needing to be cut rather than engraved or scored.
- Uploading the .SVG to Glowforge, I set the design to one of our laser cutters and set it to cut, making sure that the ventilation system was running to prevent too much smoke from the wood burning.
Milling the Acrylic
For the screen and dial, we’ll be using a sheet of 1/16 in. black acrylic to mimic the look of a blank screen. In an effort to explore as many available tools and machines as possible, we will be using our Nomad 3 CNC Milling machines to cut out these pieces. You can certainly use a laser cutter or even safely using an X-Acto knife, but this will get us more comfortable with more machines here at TPZ.
- Open up Carbide Create. Following our Nomad 3 Milling Machine Tutorial, and using the 3D model as a reference, I traced an outline for the inside of the folding screen and the inner diameter of the dial slot to create a vector of our cutouts, then saving as a .c2d file.
- Secure the acrylic stock to the bed of the Nomad 3 and connect to your computer. Uploading our .c2d file to Carbide Motion, we’re able to send instructions to the Nomad 3 to mill out our pieces.
- Make sure to follow the Nomad 3 tutorial, it goes much deeper into the safety and instructions of using these machines.
Creating the Buttons
As seen on the original screen-used prop, the keypad has text printed on the white buttons, for numerical and directional designations, along with a large button to summon Miss Minutes. While it is possible to model or paint these details onto the buttons, we can also implement one of our Cricut Maker 3 Vinyl Cutters to create the decals.
Applying the Decals
Now that we have our buttons, wooden rims, and decals, we can begin putting our buttons together for final assembly.
- We’ll start by applying the decals. Using an X-Acto blade, carefully remove the number labels from the vinyl sheet one by one as you slowly and carefully apply them to the surface of the number buttons. No need to be forceful, they’re basically stickers.
- Repeat this for all number buttons and our N, S, E, and W buttons
For the Miss Minutes and LATITUDE / LONGITUDE buttons, we’re actually going to approach this differently. These pieces are made up of many small labels that would be very difficult to align if we did them one by one, so instead we’re going to use the negative as a stencil.
- Remove the entirety of the two stickers and apply them to the button surfaces. Using your X-Acto blade, carefully remove the cutouts that we want to remain black.
- Once the details are removed, we can now use the negatives as a stencil and spray them with the same black spray paint used earlier. Once they’re dried, you can peel them off and now the decals are ready.
Gluing the Wooden Rims
Finally we can finish our buttons by adding the wooden rims.
- To attach the wooden rims to our buttons, scrape off the paint along the edges of the buttons. Doing so will give us a stronger bond between the glue and pieces.
- Apply a small bit of super glue onto the edges, making sure not to get some on the face of the buttons.
- These pieces are small, so they won’t need more than a drop.
- Place the wooden rims onto the button edges and let the glue set. Repeat these steps for all direction buttons and our Miss Minutes button
Once all rims are glued, the buttons are ready for final assembly!
Cutting the Vinyl Decals
- The decal files were created in Adobe Illustrator. To go over some of the basic tools and elements of Illustrator, follow our Illustrator Glowforge Keychain Tutorial or our Illustrator Guide for any general questions.
- Measuring the size of the buttons and finding a font that closely matches the original, type out the text decals for the number and directional buttons.
- For the Miss Minutes decal, we use the rectangle, ellipse, and line, and curvature tools to replicate the cartoon clock face on the face of the button.
- Once we have our design ready to go, we are now able to save it as an .PNG file and upload it to Cricut Design Space.
- Following our Cricut Tutorial, we are now able to cut out our decals and set them aside for assembly.
Assembling Your Parts
At this point, we have fully prepped, finished, and painted our 3D printed pieces, and cut all our acrylic, plywood, and vinyl pieces. Now is arguably the best part of the fabrication process: the end. Specifically, the final assembly, where we can see all our hard work finally come together into a final product. All our hard work has led to this stage, so let’s get right into it.
Assembling the Time Turner
We can start off our assembly with probably the easiest part, the Time Turner. This piece consists of only one 3D printed piece, two small wooden panels, and a small acrylic disk. All we need to do is glue them down.
_Acrylic_Disk.gif?w=331)
_TT_Wood.gif?w=331)
- Carefully using a knife or sandpaper, scrape/sand off some paint from the spot where you will be gluing the disk. Make sure to get down to the raw plastic so the glue sticks to that rather than just the surface of the paint.
- You can also tape any spots that where you plan to apply glue at the beginning of the build before any priming and painting.
- Note that the more paint you layer on, the harder the tape will be to remove at this stage.
- Once you have a good bit of exposed plastic, you can apply a bit of super glue onto the surface. Try not to put too much, just a little bit will get the job done
- Slide the disk into place and press down fully to ensure it adheres well.
- You may notice the disk getting hot at this stage. Super glue releases heat as it sets, so no need to worry. Just make sure you don’t burn yourself
- Repeat all these steps for the wooden panels, and once they’re glued the Time Turner is done!
Assembling the Keypad
Now we’re at the most complicated piece of the build: the keypad. Made up of various buttons and panels, this piece is what makes up a bulk of our build. Thankfully, the assembly process is still very straightforward.
- After scraping all surfaces you plan to attach all the pieces, apply a small drop of super glue to the holes modeled in for our push buttons. If you put too much you may end up gluing the button down and it can’t be pushed.
- Using the tip of an X-Acto knife, gently place the rubber buttons (recycled from a broken laptop) into the slots to stick them down. Hold them in place for a couple seconds to get a proper adhesion, and slowly pull the knife away.
Once all the rubber buttons are in place, we can now glue the wooden panels in place.
- Starting with the small panel, apply a little bit of glue and press the panel into place.
- For the bigger panel, apply more generous lines of super glue where the parts will connect. No need to flood the piece, just a little more to hold it in place.
- Make sure all the wooden pieces are fully pressed down into place to make sure everything is level and adheres well.
Now that the wooden panels are in place, we can glue the buttons in place.
- Applying a tiny drop of super glue on the top of the rubber push button, gently align and place the buttons on top.
- Make sure that they can still be pushed down and spring up, and won’t fall off.
- Repeat for all buttons, making sure they’re all in the correct order and are still pushable.
With the buttons secure, we can attach the button panels to the keypad.
- Apply two small dots of super glue to the side panel slot and drop the panel into place.
- For the direction panel, apply a couple dots of super glue in the empty spots without getting too close to the buttons, and a line across the bottom, and drop the panel in place.
- For the number panel, we don’t have much room in the panel slot to apply glue without potentially gluing the buttons shut. So instead, we’ll apply a small dot in each corner to minimize spill over.
_Rubber.gif?w=331)
_Wood.gif?w=331)
_Buttons.gif?w=331)
_Panels.gif?w=331)
Once all panels are in place, make sure all the buttons are still pushable and secure. Once that’s done, the keypad is finally assembled and done!
Assembling the Screen Lid
The last piece we need to assemble before bringing everything together is the screen.
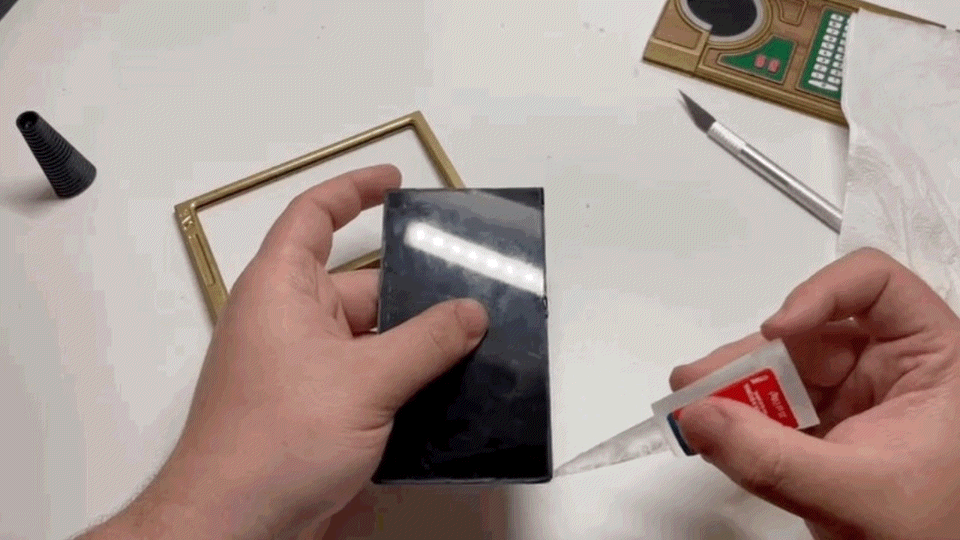
- Using a knife or sandpaper, scratch/scrape the edges of the black acrylic screen
- The smooth black acrylic is not going to grab onto the glue as strongly as a scratched up surface would. Scratching the acrylic ensures a stronger bond.
- Using either super glue or 2-part epoxy, apply a couple dots of your adhesive to the scratched edges of the acrylic. Be careful not to overflow the glue, it could seep onto the screen where we want it to be smooth
- Slide the screen into the slot, making sure not to stop prematurely and accidentally allow the super glue to set before its in place (for this reason it may be best to use 2-part epoxy).
Final Assembly
The last thing we need to do in order to assemble everything is to cut out and glue our hinge rod into place.
- 🚨 BE VERY CAREFUL AT THIS STAGE 🚨
- Wear all face protection when cutting the rod as sparks may fly towards your face
- Do not let the blade get too close to your hands or clothes. Use some sort of clamps or pliers to hold the rod when cutting
- DO NOT wear gloves while using the rotary cutter. They can get caught in the blade and injure you.
- Putting our top screen and keyboard together, insert one end of the steel rod until you meet the end of the hole. Mark the length of the rod with a sharpie and repeat on the other side
- Using a rotary cutting tool, carefully cut off each end of the rod at the mark you made, and dip them in room temperature water to cool them off after cutting.
- Once you have both ends of the rod cut, test fit them in just the keypad piece, detached from the screen, so you can see if its the right size.
- Once you’ve confirmed that they’re cut to the right size, put a tiny bit of glue at the very end of the holes on the keypad. We only want some in the very end to anchor the rod in place, too much and the whole piece may end up glued shut when assembled.
- Place the screen into place. Using pliers, slide the rods into place, making sure the ends are flush with the ends of the prop and they reach the end of the holes.
Once you’ve assembled all these pieces, give it one last test by opening and closing the screen to make sure the hinge is still freely moving. If all looks good, then well done! You know have a final product, and the knowledge to go through post-processing on any and all future 3D printing projects you take on!